Applying a Manufacturing Mindset to Recruiting
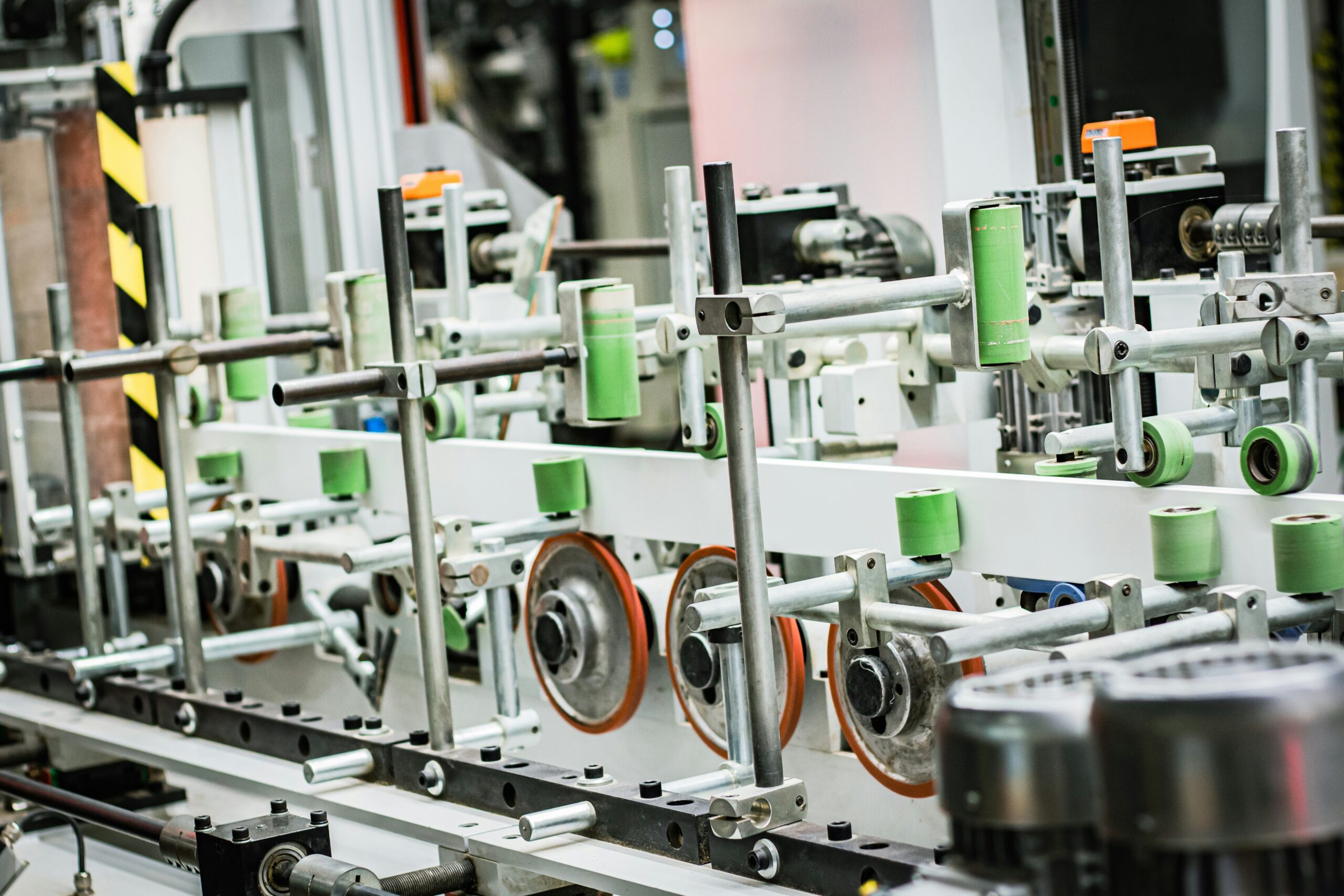
After several years of turbulence brought on by massive supply chain disruption and global competition, manufacturers are in an era of growth and innovation.
The industry is getting a lot of attention thanks to new legislation. The IIJA, IRA, and CHIPS laws are infusing more than $2 trillion through federal funding and tax incentives into multiple industry subsectors. The semiconductor, medical device, and automotive (thanks to electronic vehicles) categories are experiencing the biggest growth.
At the same time, technology is reshaping plant floor operations. According to a Gartner report, 54% of manufacturers plan to increase their technology spend this year. These efforts are largely focused on increasing efficiency, driving supply chain resilience, and preparing for sustainability requirements.
How can manufacturers execute on their ambitious plans? It takes the right workforce. Unfortunately, what has not changed is the industry’s massive talent shortage.
Talent acquisition teams within the space have long struggled to fill roles. According to NAM’s Q4 2023 Manufacturers’ Outlook Survey, more than 71% of manufacturers rank the inability to attract and retain employees as their top challenge.
The numbers don’t lie – more workers are leaving the industry than joining it. In 2023, a quarter of the manufacturing workforce was older than 55, and it’s not seen as a tempting career path for new (and younger) talent. Because of this, The Manufacturing Institute and Deloitte predict 2.1 million jobs will go unfilled by 2030.
Manufacturing companies will need a talent acquisition strategy that can accommodate their continued evolution, amid significant economic uncertainty and market change.
We recommend they look no further than their own processes to create a hiring strategy that aligns to their business. Here’s what applying a manufacturing mindset to a company’s recruiting practices looks like.
Standardize and optimize operations. Standardization drives productivity, efficiency, consistency, and predictability – all crucial on the plant floor. On a manufacturing line this means analyzing each step of the process to find areas of opportunity. Just as crucial is ensuring processes are optimized to reduce waste, promote economy of motion, and mitigate stoppages.
Manufacturers need to deliver the right product, at the right cost, at the right time. And TA teams? They need to analyze and then optimize their recruiting process to find the right people, at the right cost, at the right time.
Creating standard recruiting practices is critical to establishing a positive employer brand in the market, which helps companies attract high-quality talent to their companies. Inconsistent communication, process delays, and any other hiring missteps can send candidates looking for work elsewhere.
Also, a company’s recruiting processes are now made public via online job seeker forums and employer review sites. They must deliver a consistent, unbiased experience for all candidates in order to meet expectations – similar to how a manufacturer’s customers must all receive the same product experience.
What should TA leaders standardize? Communication methods and timetables, interview practices, and the onboarding experience, to start.
Digital transformation. In a world of continuous innovation, manufacturers must constantly adjust their processes to incorporate the latest best practices and technologies. Capturing the cost and efficiency benefits of automation in particular allows companies to weather difficult times or re-invest back into their business to create competitive advantages.
It’s survival of the most innovative.
Recruiting teams must do the same. Their processes must evolve to make it easier to connect and communicate with candidates and hiring managers. That includes everything from automated interview reminders to reporting dashboards to track critical hiring metrics.
Consumers are demanding innovation from companies, from clean cosmetic products to fuel-efficient or electric vehicles. Candidates want innovation from TA processes in the form of an intuitive, seamless hiring experience.
Supply chain resilience. The pandemic exposed costly supply chain gaps and risky practices that manufacturers have been working hard to overcome ever since. One of the biggest challenges right now, and one we referenced in our introduction, is a shortage of semiconductors and other electrical parts needed for today’s digital products.
Technology plays a big role here, too. Deloitte found that 76% of manufacturers are using tech to create transparency within their supply chains. A fewer percentage are experimenting with metaverse technologies and creating digital twins of their supply chains, for example.
TA leaders should think of their talent pipeline like a supply chain, and build resilience into it as well. Employers don’t have the luxury of raising their hand whenever they have a talent need and being able to fill the role accordingly. Talent shortages and skills gaps that prevent that from happening.
Some tactics to consider include widening the talent pools by loosening job requirements, auditing wages and benefits to ensure they are competitive, and placing a greater emphasis on skills and training.
Manufacturers will need to be adept at managing through periods of business change. The speed of economic, corporate, and technological change is only accelerating. Manufacturers will need to evolve right alongside these factors, and that takes having the right talent to move them into the future.